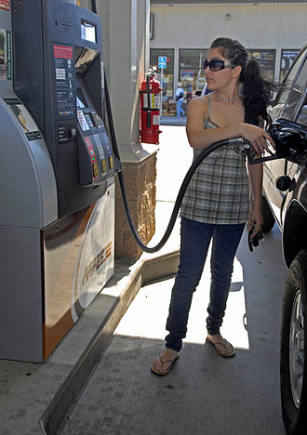
Among molecules, ethanol is one of the simplest: Two carbons, six hydrogens, and a hydroxyl group. And like other simple molecules such as water, it plays a central role in our modern world. It is one society's oldest and most popular psychoactive drugs still in use, and it's also a widely used solvent and fuel. In fact, more ethanol is used as a fuel additive than for any other purpose. According to the US Energy Information Administration (EIA), ethanol fuel use in the U.S. has increased from about 1.7 billion gallons in 2001 to about 12.9 billion in 2012.
An appealing alternative to gasoline? Not so fast.
One of the appeals of ethanol as a fuel is that it can be produced from renewable plant material such as corn, sugar cane, cassava, or grasses. Compared to petroleum-based fuels, using ethanol can also reduce oil dependence and greenhouse gas emissions.
But there are drawbacks. There is an ongoing debate about the advantages and disadvantages of replacing gasoline with bioethanol. For example, using arable land to crops like corn and sugar cane for ethanol production could lead to higher food prices. And questions remain about whether or not the energy that goes into ethanol production and the greenhouse pollution generated by the natural-gas based production process justify the cost.
With these concerns in mind, many in the industry are looking to cellulosic ethanol production for a more sustainable solution. So far, efforts have focused on making ethanol from the cellulose in plant waste such as corn stalks, wood chips, and lawn trimmings, which are inexpensive and plentiful. Cellulose can be broken down into fermentable sugars by digesting it with enzymes or by gasification. But the most difficult-and expensive-part is removing the cellulose from lignin, a complex polymer of aromatic alcohols that tightly cements the elements of plants together.
"Designer" lignin may hold the answer.
Researchers in the United States and Canada might have solved the problem by genetically engineering plants to produce a form of lignin that breaks down more easily than the natural version, making it possible to produce biofuels for a fraction of the cost of current cellulosic production methods.
The new approach, described in a recent edition of Science, was developed by a group of scientists from the University of British Columbia, Michigan State and University of Wisconsin-Madison. Basically, it involves inserting a piece of code isolated from a Chinese herb into the DNA of a poplar tree. The code alters the chemistry of some of the lignin bonds, resulting in a sort of "designer" lignin, which could make it easier to release the cellulose sugars from the plant materials.
Removing naturally occurring lignin from plant materials for the production of bioethanol and paper products requires processing caustic chemicals and high heat-about 170° C for several hours. When pulverized and subjected to a dilute alkaline treatment at 90°C for three hours, the genetically modified poplars released up to twice as many sugars as natural poplars under the same conditions. These results indicate that the "designer" lignin falls apart more easily, even though the strength of the living altered popular tree is the same at that of naturally occurring trees.
As the authors of the paper point out, the test released only a small percentage of the total sugars available in the plants. To prove that the "designer" lignin can transform the economics of the biofuels industry, the researchers must now demonstrate efficiency gains that could be gained by using these transgenic in biorefineries where 100% of the sugars are released and converted into fuel.